Comunicación presentada al VI Congreso Ciudades Inteligentes
Autor
Carlos Pajares Ortiz, Director de Operaciones y Transformación digital, Thyssenkrupp Elevadores Iberia
Resumen
Hemos unido por un lado la experiencia y el conocimiento de un equipo de técnicos, por otro la tecnología digital disponible como el IoT, Machine Learning, Big Data, etc., para modificar los procesos propios del negocio, de manera que podamos ofrecer un servicio asistido inteligente. En este proceso, por una parte, se ha integrado la información que generan diferentes dispositivos, que monitorizan y recogen los datos de los ascensores, escaleras mecánicas y rampas, para procesarlos y enviarlos a la nube. Por otra parte, se ha digitalizado y automatizado la cadena de suministro y logística, desde la producción hasta la entrega, lo que permite el envío de los repuestos necesarios para cada una de las intervenciones al equipo de técnicos de la compañía, directamente a sus vehículos o a un punto de conveniencia acordado, facilitando la movilidad y evitando desplazamientos innecesarios.
Palabras clave
Machine Learning, IoT, Big Data, Logística, Movilidad
Innovación digital al servicio de la movilidad urbana
Los ascensores son el medio de transporte más usado y más seguro del mundo. Cada día 12 millones de ascensores desplazan a más de mil millones de personas en todo el mundo. Se trata de una industria de más de 44.000 millones de dólares al año.
Con los niveles de conectividad que hay en la actualidad, era absurdo que la industria de los elevadores se mantuviese al margen. Desde 2007 hay más dispositivos conectados y habilitados para Internet, tales como ordenadores de sobremesa y portátiles, teléfonos móviles, tabletas, que personas. Y esta tendencia continúa: en 2020 ya estarán conectados 50 mil millones de aparatos para 7,6 mil millones de personas; lo que significa, 6,58 unidades por persona.
Esto ha llevado a perseguir con más fuerza su visión: innovar y digitalizar la industria del ascensor para hacer de las ciudades los mejores lugares para vivir. A raíz de ello, se ha apostado por la revolución en tecnología y transformar una industria en la que apenas ha habido cambios en más de 150 años. Para ello, se han desarrollado nuevos e innovadores productos con el fin de conseguir ese objetivo, llamando a esta transformación: Movilidad 4.0.
El proceso de digitalización va en dos líneas; la primera de ella, beneficiarse del IoT para sus productos incorporando en los ascensores sensores y dispositivos que mejoren el funcionamiento, y por otra parte la digitalización operativa de los procesos de negocio con el objetivo de ganar una mayor eficiencia y productividad, ofreciéndoles a los clientes un servicio mejorado que va desde la mayor disponibilidad de uso de su elevador hasta un mantenimiento predictivo del mismo.
Punto de partida
Explicamos brevemente el proceso tradicional para reparar un ascensor averiado con necesidad de un repuesto:
- El ascensor se avería, el cliente llama al Contact Center y el técnico acude a la instalación.
- Localiza la pieza que ha fallado y si puede la repara. Si no es posible repararla o está inservible, identifica la misma.
- Llama a su supervisor para que este, a través del catálogo de repuestos, realice el pedido correspondiente.
- Una vez realizado el mismo, se tramita en el almacén central y se envía al almacén de la delegación.
- Una vez allí, se localiza al técnico para que se desplace a la delegación y recoja el repuesto correspondiente.
- El técnico acudirá a la instalación para cambiar la pieza averiada y dejar la instalación en marcha.
- Para realizar todo este proceso se requiere un tiempo considerable, puesto que es bastante “pesado”.
Pero, ¿qué les parecería cambiar la forma en que se presta el servicio a los clientes y centrarse realmente en un servicio de excelencia hacia el cliente y que lo percibiera?
¿Qué pasaría si …
- … el técnico de mantenimiento pudiera pedir piezas de repuesto a través de un catálogo de repuestos en una aplicación y las piezas de repuesto pudieran llegar a un punto de entrega previamente acordado?
- … aún más, que el técnico pudiera saber cuándo podría estar disponible el repuesto?
¿Qué pasaría si …
- … el técnico pudiera tener soporte online para solucionar averías?
- … el sistema pudiera saber cuál será el próximo componente a sustituir y, de este modo cambiarlo por adelantado?
¿Qué pasaría si …
- … el sistema pudiera confirmar de antemano el pedido de repuestos automáticamente, enviar una alerta al dispositivo móvil del técnico y, de este modo, el técnico pudiera recoger el repuesto en el punto de entrega convenido y evitar la avería?
- …existiera un sistema de planificación de la demanda automatizada que aprenda del histórico, me envíe los repuestos sin que yo los tenga que pedir?
Soluciones aplicadas
En nuestra compañía ha sido posible gracias a la transformación digital de los servicios, a través de los proyectos llamados Spare Parts Business Excellence (SPBE), de MAX, sistema de mantenimiento predictivo y DataEvo (programa de movilidad para el equipo técnico)
La digitalización ha sido esencial para la integración de todas las operaciones propias del negocio de servicios. Todas las operaciones están trazadas e integradas en los sistemas, formando del entorno digital y aprovechándose de las ventajas que nos ofrece el IoT. Todo está relacionado, conectado y secuenciado debidamente. Gracias al BIG DATA se aplica el proceso o procedimiento adecuado en cada momento en función de unas necesidades concretas y una vez tratados los datos.
La clave principal reside en la conexión inteligente de los diferentes datos y sistemas, de manera que se puedan aplicar los algoritmos adecuados; eso es Internet de las Cosas (IoT) y Machine Learning (ML).
En el negocio de servicios en el sector de la elevación para completar este proceso, es imprescindible ejecutar el mantenimiento predictivo. El objetivo último es eliminar casi por completo el mantenimiento correctivo. Este tipo de mantenimiento correctivo no será necesario, puesto que gracias al dispositivo IoT instalado en el ascensor, se ha anticipado cualquier avería que pudiera ocurrir en los sistemas y el ascensor estará siempre en servicio y en condiciones de funcionar.
El objetivo de lograr una mejora continua en la prevención de fallos ha llevado a la compañía a desarrollar un dispositivo basado en el IoT como primera solución de mantenimiento predictivo para ascensores y escaleras mecánicas, que combina Big data, cloud computing y machine learning, para consolidar todos los datos sobre los ascensores y escaleras y reducir el tiempo de inactividad del ascensor a la mitad, lo que conlleva un aumento significativo en la disponibilidad y eficiencia de las ciudades.
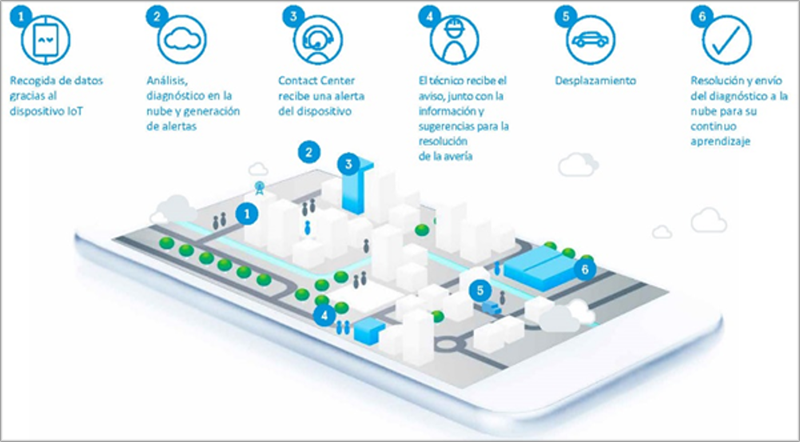
Con nuestro dispositivo desarrollado internamente y que se vale de IoT, los ascensores están conectados a Azure, la nube de Microsoft, lo que permite un control preciso de todas las funciones, como la velocidad de funcionamiento, los mecanismos de las puertas, los viajes realizados. Todos los datos son analizados a través de un algoritmo único que envía diagnósticos precisos directamente al técnico; a su herramienta de movilidad. De esta manera, convierte en realidad que un ascensor pueda «contarle» sus necesidades reales a los técnicos de mantenimiento y advierta de aquello que funciona fuera de unos patrones establecidos.
A través del machine learning, el dispositivo es capaz de predecir los problemas que podrían aparecer en el ascensor, antes de que estos ocurran y avisará de la necesidad de sustituir sus piezas y componentes antes de que termine su ciclo de vida. Además, con esta información, los clientes pueden comprobar el estado del ascensor con total comodidad y transparencia, permitiéndoles planificar con suficiente antelación las reparaciones necesarias.
El proyecto se completa gracias a la conectividad de los ascensores con las operaciones, lo que permite que los técnicos de mantenimiento conozcan en tiempo real el estado de las instalaciones a las que deben atender. El dispositivo IoT forma parte los procesos de Industria 4.0 al realizar transformación digital sobre una maquina activa.
Planificación y automatización de la cadena de suministro
Otro aspecto crucial en la gestión integrada de los servicios es la planificación de los repuestos para tenerlos disponibles en el momento necesario y en el lugar preciso. Para ello, es imprescindible la centralización de la gestión de los repuestos y disponer de una demanda fiable y planificada.
¿Cómo funciona?
Toda la cadena de suministro se activa en el SBC (Spare Business Center) almacén central y torre de control, donde el equipo responsable de planificar los inventarios para el próximo mes se ayuda de la herramienta de demanda planificada (Prophet), una herramienta de análisis automatizado de la demanda, configurando la lista de repuestos necesaria para cada técnico en función de su consumo y de la tecnología de los aparatos en su ruta habitual.
En base a esta previsión, los operarios del almacén incluyen todos los materiales necesarios en un contenedor de reparto (“tote”), etiquetado con un código QR y lo envían directamente a un punto de conveniencia designado por el propio técnico. Un mensaje de móvil le alerta de que ya lo tiene disponible. Cuando lo recoge, solo tiene que escanear el código QR y todos los materiales enviados se añaden directamente a su inventario digital.
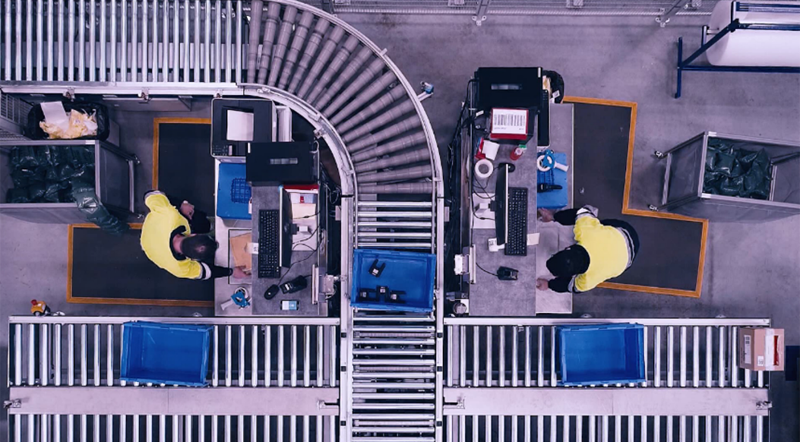
De este modo, cuando el técnico llega a un ascensor averiado instala las piezas, previamente escaneadas con su aplicación de movilidad, DataEVO, y estas se restan automáticamente de su inventario. La información sobre los repuestos consumidos es procesada y analizada por el equipo de planificación del Spare Business Center (SBC) que reconfigura dinámicamente las necesidades en función de la demanda, mejorando así las previsiones futuras.
La compañía es pionera en enviar los pedidos de reposición automáticamente al equipo de técnicos de mantenimiento, esto significa aproximadamente multiplicar por 4 el volumen de gestión anterior en Spare Business Center, pero reducir la gestión en las delegaciones y, por lo tanto, minimizar los errores.
Para ello, cuenta con un nuevo espacio logístico de más de 6.000 m2 situado en San Fernando de Henares, uno de los principales ejes logísticos de Madrid, donde se encuentran todos los operadores logísticos.
El centro logístico está equipado con la última tecnología. Las referencias quedan repartidas en diferentes zonas según su tamaño y el ABC de movimientos, haciendo que las referencias de mayor rotación queden más cerca de la zona de expediciones. Dentro de esta distribución, una parte esencial es el almacén automático, que se ubica en el eje central de la instalación y que tiene una capacidad para almacenar más de 9.000 referencias. Este almacén automático está dotado con un transelevador viaspeed con la última tecnología que permite velocidades de 6m/s en traslación y 3 m/s en elevación, a la vez de estar dotado de un sistema de recuperación de energía en la frenada, que se entrega de nuevo al motor, cuando este lo demanda.
En uno de los laterales del almacén automático quedan expuestas las 305 referencias de mayor rotación en un sistema pick by light. Estas referencias son alimentadas directamente por el transelevador. El picking del resto de referencias se realiza en la cabecera del sistema automático mediante un sistema put to light, o en el almacén convencional mediante carretilla recoge pedidos.
Para reagrupar las piezas pertenecientes a un mismo pedido pero que proceden desde diferentes áreas del almacén, se ha previsto un sistema tipo “sorter” que hace llegar las diferentes piezas en el orden correcto a un puesto de consolidación, donde un operario prepara el pedido para su envío.
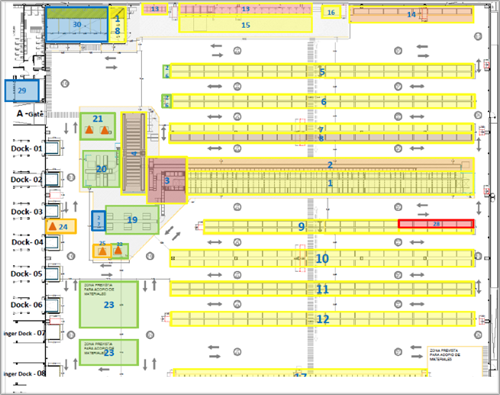
En los casos en que sea necesario, se realizará una segunda consolidación de pedido con los materiales extra dimensionales procedentes de las áreas manuales del almacén.
Todos los procesos dentro del almacén, desde la recepción, el chequeo de peso y dimensiones con un “cubiscan”, así como el registro del nuevo código si no existiera previamente, ubicación de la mercancía, picking, consolidación de pedidos y preparación para su envío, están controlados por un Software específico de gestión de almacenes, que está 100 % integrado con el ERP del nivel superior: SAP.
Minimizamos los tiempos de espera y maximizamos el uso de los ascensores (disponibilidad cercana al 100%), gracias al mantenimiento predictivo y la disponibilidad de los repuestos necesarios antes de que el ascensor se averíe.
El proyecto SPBE (Spare Parts Business Excellence) nos da una idea de la transversalidad necesaria en los procesos de la Transformación Digital.
Beneficios obtenidos
La puesta en marcha de todo este conjunto de medidas ha supuesto en primer lugar, un aumento de la disponibilidad de los ascensores que la compañía tiene en su cartera de mantenimiento, lo que redunda en la satisfacción de nuestro cliente. Según las encuestas del NPS más de un tercio de nuestros clientes también son nuestros promotores.
El proceso de centralización y automatización del almacén ha permitido que la compañía pueda optimizar el stock del almacén y realizar su redistribución de los repuestos geográficamente en función de las necesidades de sus técnicos de mantenimiento. Este hecho significa que progresivamente se está produciendo una reducción del nivel de stock de la compañía de hasta un 30%. A ello se añade una constante optimización en todos los acopios de la compañía. El análisis de los Big Data, permiten a la compañía anticipar la compra de los materiales necesarios para el mantenimiento de instalaciones de elevación previendo cualquier rotura de stock y garantizando en un 98% la disponibilidad de ascensores y escaleras mecánicas. En este mismo sentido, el proceso de centralización y automatización ha incrementado el nivel de servicio a un 92%, medido en OTC (On time and Complete) de las expediciones de repuestos a los técnicos de mantenimiento. En definitiva, la compañía tiene una visibilidad y trazabilidad END to END en la cadena de suministro, lo que en cifras significa que se ha reducido un 30% en horas laborales dedicadas a los procesos para invertirlo en otras tareas de mayor valor añadido.
Desde el punto de vista de la sostenibilidad y cumpliendo con los Objetivos de Desarrollo Sostenible de las Naciones Unidas, el 50% del embalaje de los envíos de repuestos a los técnicos de mantenimiento de la compañía han sido sustituido por contenedores de reparto sostenibles y reutilizables. A ello se une que los envíos, tanto de reposición como de los repuestos urgentes se envían directamente al punto más conveniente para los técnicos de mantenimiento, lo que redunda en la reducción de 62 Tn de CO2 emitidas anualmente, en una flota de más de 1.700 vehículos, además de la disminución del tiempo necesario para desplazamiento mejorando la seguridad de las operaciones al reducirse las horas de conducción.
Conclusión
Gracias la transformación y digitalización de la compañía se consigue la excelencia en sus servicios y, por ende, la satisfacción de sus clientes debido a que los ascensores y escaleras mecánicas tienen una disponibilidad de un 98%, estando en continuo funcionamiento sin interrupciones.
Agradecimientos
Quiero agradecer a todo mi equipo por su implicación en este proyecto. Pero especialmente a Ignacio Perez Bermejo, David Jimenez Ortega y Abel Caja, responsables individuales de los distintos proyectos y ser capaces de integrar todos los procesos para que la Digitalización para Smart Services sea un éxito.